- FE News»
- PPS News»
- Apr. 18, 2025
- Holiday Closing Notice [Spring 2025]
- Oct. 31, 2024
- [News Release R-1020] Release of "ECHELON Zen-Xero DYNAMIX”
- May. 15, 2024
- [News Release R-1019] Release of "ECHELON Ver.3.0”
- Oct. 02, 2023
- [News Release R-1018]Compound that achieves a genuine finish Full Renewal of “KATANA” Series
- Jun. 27, 2023
- [News Release] A final finishing compound that achieves a beautiful wet gloss. "KATANA DARK-SHOT" is Released.
Light lens structure
1. Injection molding
Like other plastics, heated "pellets" (the raw materials) are injected into a mold and molded into various shapes.
2. Annealing (stress relieving)
This is a process that prevents a molded lens from returning to its original shape by applying heat treatment to it in a furnace for a certain period of time.
3. Cleansing degreasing
Oil and contaminants from the molding process are removed by degreasing them with boiling water followed by drying.
4. Application of hard coat
Using a UV-curable coating suitable for polycarbonate that contains little organic solvent, a weather-resistant coating is applied to the surface of the lens to prevent discoloration and scratching caused by ultraviolet rays.
5. Ultraviolet irradiation
The coating is cured by irradiating it with ultraviolet rays (UV).
6. Drying
Trace amounts of organic solvents are removed.

Completion
The key point for weather resistance in this process is the presence of the hard coat. The addition of the hard coat to the surface of the polycarbonate provides thorough weather resistance and enhances the quality overall. Generally, the headlight's hard coat is between 5 and 10 microns thick, with a surface hardness of 3H to 4H. The most important feature is the high weather resistance towards ultraviolet rays.
Clear coating for automobiles | Clear coating for headlights (hard coat) | |
---|---|---|
Coating thickness | 20–30 microns | 5–10 microns |
Hardness | H - 2H | 3H - 4H |
You can see that clear coating for headlights has a higher hardness and approximately half the thickness of clear coating for automobiles. However, it would be difficult to work out how to solve the problems that occur based on the hardness and thickness in this table alone. Accordingly, in the next section, we will examine what kind of phenomena actually occur and carry out tests on scratch resistance and solvent resistance.
Headlight solvent resistance test
1.Silicone Off
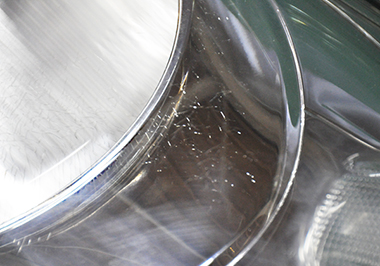
When the oxide film on the surface is removed, the hard coat deteriorates, which leads to the polycarbonate itself cracking. It is thought that, as the deterioration of the hard coat progresses due to ultraviolet rays, the polycarbonate material itself also begins to be affected by those rays.
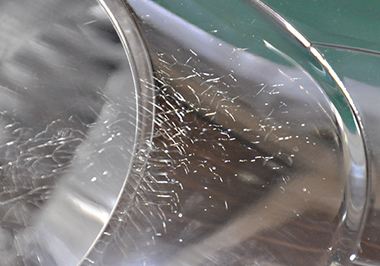
You can see that countless fine cracks appear after wiping the surface with Silicone Off.
2. Lacquer thinner
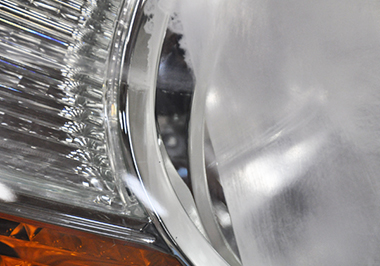
You can see that wiping the surface with lacquer thinner, a powerful solvent, causes the surface to dissolve and become cloudy.
3.Alkaline detergent
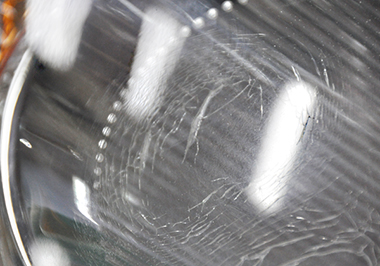
The deterioration of the polycarbonate has progressed and cracks have formed.

You can see that spraying strongly alkaline detergent onto the surface causes cloudiness and drastic enlargement of the cracks.
As you can see, one factor in the deterioration of headlights is the weakness of polycarbonate towards solvents, alkaline detergents, strongly acidic solutions and so on. The raw material for the polycarbonate resin used in headlights is made by only a few companies around the world. While we have not been able to test each company's product, we believe the same phenomenon occurs in all of them.
Headlights: Contents
Related products