- FE News»
- PPS News»
- Oct. 31, 2024
- [News Release R-1020] Release of "ECHELON Zen-Xero DYNAMIX”
- May. 15, 2024
- [News Release R-1019] Release of "ECHELON Ver.3.0”
- Oct. 02, 2023
- [News Release R-1018]Compound that achieves a genuine finish Full Renewal of “KATANA” Series
- Jun. 27, 2023
- [News Release] A final finishing compound that achieves a beautiful wet gloss. "KATANA DARK-SHOT" is Released.
- May. 22, 2023
- [News Release] Full renewal of buffing pad category Brand integrated into HAYABUSA
Weather resistance of anodic films
As you can see, the material varies between countries, but one would expect that both materials have been sufficiently processed for weather durability. Nonetheless, in reality, anodized aluminum moldings in European cars frequently begin to deteriorate. So, what is causing the deterioration of these European cars in Japan? One reason is that anodization itself can only provide limited protection. The durability of the anodic film will vary depending on the treatment process, as well as the composition and thickness of the aluminum base. In addition, the characteristics of standard anodization without coloring differ from color anodization.
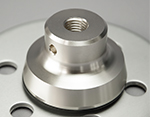
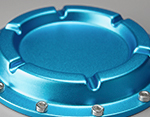
When kept clean and well-ventilated, anodized moldings have considerable weather resistance and corrosion resistance. However, like painted surfaces, moldings on the outside of a vehicle are inevitably exposed to a variety of contaminants. If such contaminants (silica scaling, dust and oil from the air, limescale, salt) are left on the aluminum, the molding will gradually begin to corrode and cracks will form due to differences in the thermal expansion coefficient of the aluminum base and anodic film. The contaminants will then permeate those cracks and take hold. This effect is particularly severe with acidic or alkaline contaminants. Another probable reason is that there are differences in the techniques used for the anodization process. To look at it from another perspective, Europe, where the vehicles are manufactured, has low temperatures and low humidity, while Japan, where the vehicles are used, is hotter and more humid. As such, the climate and environment may also play a role. This can also be seen in, for example, electrical appliances like household refrigerators. The cooling method of Japanese refrigerators fundamentally differs from European refrigerators due to differences in climate and humidity. This kind of deterioration due to physically unavoidable contaminants, despite the presence of a protective anodic film, can be attributed to the properties of metals. When two different metals are connected and in contact with water due to rain or moisture, one metal will become positively charged, and the other negatively charged. This is similar to a battery with a short circuit between the positive and negative ends. In that state, aluminum, which already ionizes easily, tends to corrode more quickly. Once the corrosion begins, it progresses deeper into the material due to a synergetic effect with the contaminants. This phenomenon cannot be prevented by anodization, and seems quite likely to occur in an automobile made using various materials.
What is anodization?
Aluminum naturally forms a thin oxide film on its surface. Anodization is an artificial process that thickens that film to provide improved resistance to corrosion and wear. The thickened film is called an anodic film.
Structure of anodic film

(1) Barrier layer
The barrier layer is a conductive film formed in the early stages of electrolysis that supports the formation of a porous film on top of it. In other words, it is the location where a porous layer forms in reaction to the oxygen released by dissolution of the aluminum at the base of the barrier layer through electrolysis. As the porous film forms, the bottom of the barrier layer moves down, but the thickness of the barrier layer does not change. The thickness is generally around 20nm.
(2) Porous
The anodic film is an aggregation of these porous layers. Viewed from the top, it is a collection of hexagonal film cells with nanopores in the center. Depending on the electrolytic conditions, the cells range between 100 and 300nm in diameter, while the nanopores are between 10 and 20nm in diameter. Standard color anodizing works by filling the top of nanopores with dyes, while electrolytic coloring works by depositing metals or metal oxides into the bottom of pores.
(1) Clear anodizing
Coating thickness | 6 - 10㎛ |
---|---|
Color | Color of the aluminum material |
Purpose | Rust prevention/requirement for precise size |
(2) Color anodizing
Coating thickness | 15 - 30㎛(must be at least 30㎛ for black coloring) |
---|---|
Color | All colors possible (generally black) |
Purpose | Coloring |